Reasuransi Umum
Proses Pembuatan Semen dan Risiko pada Pabrik Semen
Semen adalah suatu campuran senyawa kimia berbentuk butiran yang tersusun dari batu kapur/batu gamping, alumina, pasir silika, gypsum, dan tanah liat. Semen bila dicampur dengan air dalam jumlah tertentu akan mengikat bahan-bahan lain menjadi substansi yang memadat dan mengeras dengan sifat seperti batu yang disebut dengan concrete (beton).
Semen diproduksi menggunakan proses kering dan basah. Ada pabrik semen yang mampu melakukan produksi semen dengan kedua metode tersebut, namun ada juga yang tidak. Proses kering pada produksi semen lebih disukai karena proses basah membutuhkan panas lebih banyak sehingga exposure fire lebih besar.
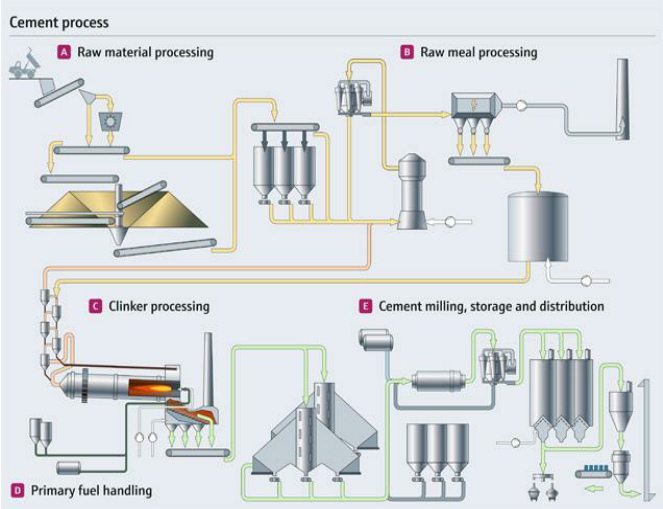
Gambar 1. Proses Produksi Semen
Sumber: https://www.researchgate.net
Secara garis besar, proses produksi semen adalah sebagai berikut:
- Penambangan dan penyimpanan bahan mentah
Bahan baku utama diekstrak dari pertambangan dengan peledakan atau dengan penghancuran menggunakan mesin berat. Kemudian bahan baku diangkut dari pertambangan menggunakan truk/alat-alat berat. Bahan baku yang berasal dari pertambangan umumnya masih dalam bentuk batuan besar, oleh karena itu dibutuhkan proses penghancuran bahan baku ke ukuran yang lebih kecil. Bahan baku kemudian disimpan dalam penyimpanan.
- Proses homogenisasi campuran
Selanjutnya dilakukan proses homogenisasi dan penambahan pasir silika dan bijih besi ke dalam campuran.
- Pre-Heating
Proses pemanasan awal dari campuran membutuhkan panas dengan suhu sekitar 500
oC dan biasanya panas yang digunakan berasal dari residu udara panas proses pendinginan.
- Calcining
Campuran selanjutnya melalui proses kalsinasi dalam kiln. Dalam proses kalsinasi, campuran dipanaskan menggunakan api langsung dengan suhu sekitar 1300
oC hingga 1500
oC. Dalam proses ini, kalsium karbonat dari batu gamping akan bereaksi dengan panas menjadi kalsium dan karbon dioksida. Kalsium kemudian akan bereaksi dengan tanah liat dan pasir sehingga terbentuklah suatu material yang disebut clinker.
- Cooling
Clinker didinginkan menggunakan fan hingga suhu di bawah 100
oC. Udara panas yang dihasilkan digunakan sebagai energi untuk proses pre-heating. Kemudian clinker disimpan sementara pada clinker storage silo.
- Mixing
Clinker dicampur dengan zat aditif lainnya seperti gipsum, abu vulkanik, dan pozzolan berdasarkan sifat semen yang diinginkan. Kemudian campuran digiling di ball mill. Setelah itu campuran disimpan dalam silo penyimpanan semen.
- Loading/Packing
Berkaitan dengan risiko, kondisi yang bisa menimbulkan risiko pada pabrik semen diantaranya:
- Risiko pada alat conveyor belt. Conveyor belt adalah alat yang mempunyai exposure terbesar dalam pabrik semen karena alat ini secara berkelanjutan menghubungkan tiap plant dan bangunan. Salah satu fungsi conveyor belt adalah untuk mentransfer bahan baku dari tempat penambangan ke roll mill. Kebanyakan bahan conveyor yang digunakan adalah rubber belt conveyor. Kerusakan pada conveyor ini cukup banyak diantaranya:
- Belt koyak diakibatkan potongan batuan dan kerikil menggesek belt atau saat batuan tersebut jatuh pada conveyor.
- Belt berjalan tidak sesuai jalur, hal ini dikarenakan badan roller yang sudah aus dan mengakibatkan belt kendur sehingga berjalan tidak sesuai jalur.
- Belt putus diakibatkan oleh naiknya temperatur pada motor, kurangnya pelumasan pada pulley dan cara penyambungan yang kurang tepat
- Corner roller tidak berputar akibat debu yang menempel dan tidak dibersihkan
- Material conveyor belt terbakar. Material conveyor belt terbuat dari rubber, leather, dan canvas yang mudah terbakar dan bisa menyebarkan api dengan cepat.
- Risiko pada alat crusher atau peralatan penghancur dimana seiring berjalannya waktu menunjukan tanda keausan yang tinggi, seperti goresan dan retakan pada breaker bar dan impact plate. Potongan batuan yang berukuran terlalu besar juga bisa menghalangi crusher rotor, yang menimbulkan kerusakan berupa goresan akibat terjadi gesekan antara batu dengan alat dan kerusakan pada roda gigi dan corong.
- Risiko pada tube mill & clinker grinder. Tube mill yang digunakan untuk menggiling bahan baku dan clinker sangat mungkin terkena kerusakan pada bagian dinding ujung (trunnion) pada bagian inlet. Selain itu, efek-efek gaya pada tube mill (bearing load dan reversed bending force) bisa menyebabkan retakan pada area radius transisi dari trunnion dan lama-lama retakan ini bisa menjadi parah bahkan membuat alat berhenti dan tidak dapat beroperasi.
- Risiko pada rotary kiln. Kerusakan sering terjadi pada kiln shell/kiln jacket, riding ring (tyre), dan support roll. Jika riding ring (tyre) dipasang terlalu ketat, kiln shell/kiln jacket akan mengkerut selama beroperasi. Sebagai akibatnya, retakan bisa terbentuk pada kiln shell/kiln jacket dan bisa menyebabkan lapisan kiln rusak. Jika kontak antara support roller dan riding ring (tyre) tidak memadai atau jika permukaannya tercemar/kotor, goresan mungkin terbentuk akibat hal tersebut.
- Risiko pada Electrostatic Filter. Ketika filter elektrostatik digunakan, perawatan khusus harus dilakukan untuk menghindari penumpukan dari karbon monoksida/campuran udara eksplosif.
- Risiko pada motor listrik yang menggerakan blower, grinding mill, dan kiln yang diakibatkan debu-debu yang masuk melalui filter udara dan menghalangi celah ventilasi dari stator winding. Pendinginan yang dihasilkan akan berkurang dan ketebalan dari isolasi bisa membuat timbulnya arus pendek pada stator winding dan merusak mesin.
- Batubara digunakan untuk pembakaran pada rotary kiln. Penyimpanan batubara harus benar-benar diperhatikan. Apabila batubara didiamkan dalam ruang terbuka maka batubara ini bisa mengalami self-combustion.
- Hubungan arus pendek atau short circuit adalah hal yang umum yang terjadi hampir disemua bangunan. Short circuit diakibatkan kurang rapinya jaringan listrik, usia bangunan/perkabelan serta housekeeping dari pabrik itu sendiri.